Concrete Repair involves fixing concrete surfaces and structures that have been damaged. The benefits of regular concrete repairs include increased safety, extended lifespan, and improved aesthetics.
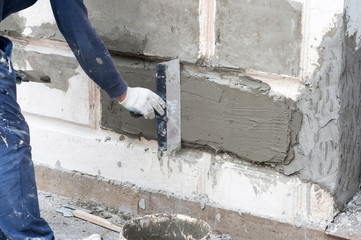
It is important to choose appropriate concrete repair methods and materials. The ideal repair material should be compatible with the host structure. Incompatibility can lead to premature failures, e.g., due to differential shrinkage or thermal expansion.
The foundation of a good concrete repair is a well-prepared surface. For this reason, the preparation process is one of the most important elements of any repair project. Using the proper cleaning, profiling and saturating procedures will help to ensure that the repair material adheres well to the concrete and remains structurally sound over time.
During this step, all dirt, oil, dust and debris must be removed from the surface of the concrete. This can be accomplished with a variety of physical methods, such as sandblasting and grinding. In addition to removing all foreign matter, this process also helps to roughen the surface of the concrete, improving the mechanical bond between the existing concrete and the repair material. This profile is standardized by the International Concrete Repair Institute (ICRI), and is designated by a concrete surface profile (CSP) number, ranging from CSP 1(nearly flat) through CSP 9(extremely rough).
Crack injection is a popular technique for repairing cracks in concrete surfaces. Using specialized polymers or epoxy compounds, crack injection fills the crack and prevents further damage to the structure. Crack injection can be applied to both wide and hairline cracks, and is ideal for repairs requiring structural integrity.
Another method for repairing concrete is to apply a specialized patching compound. This type of repair is appropriate for small, localized areas of damaged concrete. The concrete patching compounds are available in a wide range of formulations, including traditional concrete mixes, polymer-modified cements and fast-setting hydraulic cements. In addition, there are a variety of tools to help ensure that the patching compound is applied evenly.
The final step in preparing the concrete for patching is to saturate it with water. This will help to open up the pores of the concrete, and allows the coating to more easily “wick” into or “wet” the concrete when it is later applied.
Once the concrete has been saturated, it is ready for the application of a specialized primer/bonding agent. Products like SpecChem’s Strong Bond and SpecWeld act as the “glue” that bonds the repair material to the existing concrete, and ensures a solid, unified surface. These bonding agents should be applied while they are still tacky, so that they do not dry out completely before the repair material is added.
Repair Materials
The repair materials used in the restoration of concrete structures must be compatible with their substrates, and able to achieve adequate mechanical strength in a short time. It is also crucial that the repair material have low shrinkage. This is particularly important in structural repairs, where the repaired concrete must withstand shear and bending forces.
There are many different inorganic repair materials available for concrete surfaces. These include cement-based repair materials, alkali-activated materials and polymer-modified inorganic repair materials. Depending on the requirements of the concrete structure, different admixtures can be added to these repair materials to improve some of their properties such as low shrinkage and high flexural strength.
In addition to the selection of a suitable repair material, the surface preparation of the existing concrete must be carried out with care. The objective is to create a rough surface on the old concrete that improves the mechanical bond between the new repair material and the existing concrete. For this reason, several methods can be used, such as shot blasting and acid etching.
Once the concrete is prepared, it must be brought to a Saturated Surface Dry (SSD) state. This ensures that the pores of the concrete are filled with water, but the surface is not wet to the touch. This will prevent the repair material from absorbing the water from the existing concrete, which can lead to an improper cure and weak bond.
Another step that is often overlooked in the repair process is the use of a priming or bonding agent. Products like SpecChem’s Strong Bond and SpecWeld serve as the “glue” that enhances the bond between the existing concrete and the repair material. When applied while the concrete is still tacky, these products will react with the surface of the concrete to form a strong chemical bond.
Alkali-activated materials are a type of inorganic repair material made from the alkaline activation of silica (SiO2) and alumina (Al2O3)-rich materials such as fly ash, blast furnace slag and metakaolin. This material has been shown to be useful in repairing damaged concrete structures as it has good mechanical properties and good adhesion to concrete substrates [25].
Curing
In addition to ensuring that the right repair material is used and that it is applied properly, the concrete must also be well-cured. Without proper curing, the durability of the concrete repair will be compromised. Insufficient curing will cause the repair to fail and may even require that it be removed completely and replaced. During the curing process, the concrete needs to stay moist in order for the cement to develop its full strength. The curing process can be sped up by spraying the surface with a curing compound or by creating small ponds of water on the surface.
During this time, the water in the concrete will be absorbed and then re-evaporated to the surrounding air. This cycle continues until the concrete achieves its full strength. The duration of this process is influenced by the temperature, humidity and wind speed. The best way to ensure that the concrete is sufficiently cured is to provide a continuous barrier of protection. Penetrating sealants, such as silanes, siloxanes and epoxies, are an excellent choice for this purpose.
While these products offer a variety of benefits, they should not be used on their own. They must be paired with proper surface preparation to ensure that the repair material bonds well and is able to resist the loads to which it will be exposed. The proper surface preparation steps include cleaning, profiling, saturating and priming the concrete.
In the past, many projects relied on shotcrete to repair cracks and voids in existing concrete structures. While this method is effective, it is messy and can leave holes in the concrete surface. Today, contractors are using a new and more efficient approach called PolyLevel, which uses a two-part polyurethane polymer to fill voids and lift sinking concrete slabs. This technology is less invasive, faster and more cost-effective than traditional methods.
SpecChem is committed to providing not only high-quality concrete repair products, but also the tools and training necessary to help contractors use them effectively. By following the simple but critical steps of cleaning, profiling, saturating, priming and applying the correct repair material, contractors can make sure that their repairs last for years to come.
Installation
Concrete repair is an important part of the building process. It can elevate curb appeal, boost your home’s value and improve safety. But, it can also be time consuming and expensive.
To maximize the longevity of your concrete surfaces, it’s important to follow the right steps. This includes surface preparation, use of a high-quality repair material and ensuring that the surface is properly cured. It’s also crucial to take proper safety precautions, allocate enough time and money for the project and consider professional help when necessary. By following these simple tips, you can ensure that your repairs last for years to come.
The first step in the repair process is preparing the existing concrete surface for new material. This step is very important because concrete repair materials will not adhere to dirty or contaminated surfaces. This can be done using physical methods such as sandblasting, grinding or power washing, or chemical methods such as cleaning solutions or hydrochloric acid. This is necessary to remove contaminants like oil, road salts and other chemicals, as well as loose particles and surface corrosion.
Once the concrete is cleaned, it should be profiled, which helps to create a more uniform surface that will allow for better adhesion. This is done by grinding, sanding or wire brushing, or mechanical means such as using an air compressor to blow out voids in the concrete. Depending on the severity of the damage, it may be necessary to remove existing coatings or other layers of concrete. Care should be taken to avoid damaging any steel reinforcement that is embedded in the concrete or other critical components such as plumbing.
Before the concrete repair material is applied, it must be properly mixed for a lump-free consistency. For larger repair jobs, a mechanical mixer is required to ensure that the mixture is consistent and has a high-strength finish. For small repairs, a margin trowel can be used to mix the repair material by hand. The repair area should be dampened prior to application. Dry concrete robs water from the new repair material, resulting in a weak bond and shrinkage cracking.